產品簡介
自動疊合迴流拆解系統為銅箔基板及印刷電路板製程中,將銅箔、Prepreg/ Inner和鏡面鋼板自動三明治疊合成一定需求量後,經由自動物流系統輸送並蓋上上蓋板後,送入熱壓機壓合,並在壓合後自動地分離鏡面鋼板與銅箔基板或電路板,再將鏡面鋼板自動回流、磨刷清洗乾燥後,送回無塵室循環使用的系統;而承載盤則透過自動迴流系統輸送、暫存,以利疊合室取用。
於其他相關片材疊合、熱壓領域,如塑料印刷地板、裝飾板、太陽能板…等,
皆可應用本自動化疊合迴流生產系統提昇產品良率、降低操作人員負荷、降低企業成本。
LS專利型自動疊合迴流拆解系統,具備高良率、高產速、轉換製程快、易操作、換料快等優點 ,配合LS無與倫比的鋼板刷磨清洗機,助你贏在「毫釐之爭」的時代。
疊合原理【專利型】
在鏡面鋼板經刷磨清洗機進入無塵室後,立即由雙層銅箔自動裁剪機「同時」裁出上、下兩張適當尺寸之銅箔,經伺服吸取移載機,將兩張銅箔由上而下,由下而上包覆鏡面鋼板,疊合動作「一氣呵成」
相較傳統需2站式夾吊疊合,專利型立體化疊合系統,一站式成型優勢,除A. 在最短的時間內完成(銅箔+磨板+銅箔)三明治疊合的動作,提昇產速外,B.最短成型時間,更避免銅箔亮面暴露環境中受微塵粒子汙染,大幅提昇組合良率。故其驚人的良率及效率非傳統疊合方式可比擬。
另外,專利型立體化疊合系統,一站式成型搭配雙疊板設計,更可凸顯生產上高度靈活性、與高產能的特性;反觀傳統2站式夾吊疊合搭配雙疊板設計,無法改善先天設計上干涉盲點,產能僅新式立體化疊合70%生產效率。
因專利型立體化疊合設計,12um銅箔疊合不良率,更可「自動化」穩定控制於≦0.5%
特點
|
|
一、專利型上、下銅箔亮面對應創新設計,立體化疊合系統,同步送料、裁切、組合之動作方式,大幅降低銅箔亮面與磨板於環境中受污染之機會,大大提昇成品之良率
|
|
|
二、自動疊合夾吊機升降機構採「偏心輪/滾珠螺桿+伺服」驅動,升降加減速平順,定位精準,並降低無塵室內空氣擾流所造成之污染機會
|
|
|
三、銅箔送料採用伺服趨動及先進張力控制裝置,輔以靠刀式單剪裁切設計。可裁剪厚銅、薄銅與離型膜,輸送過程中,無摺痕、無粉塵汙染、無刮痕產生
|
|
|
四、無塵室體積小,易於控制無塵室落塵量品質,維持產品高良率
|
|
|
五、夾具與Prepreq/ Cu接觸面,皆採用工程塑膠,不會造成刮傷或墊傷
|
|
|
六、承載板於疊合升降輸送機上,附有左右校正及壓制功能,並於四周設有集塵口,(總集塵風量:建議 30 CMM)
|
|
|
|
專利型立體化疊合系統,一站式成型搭配雙疊板設計,更可凸顯生產上高度靈活性(左右疊板台無叫料時間差干涉問題,可配合左右疊板台疊置時間差異,左1排4,右1排6 ok,生產靈活度高)、與高產能的特性;反觀傳統2站式夾吊疊合搭配雙疊板設計,無法改善先天設計上干涉盲點(一旦有時間差,疊合順序與流暢度大亂),產能僅新式立體化疊合60~70%生產效率。
|
|
|
|
立體化設計,無塵室體積小,無塵品質控制易,且有效長期降低無塵室空調秏量,節約空調成本
|
|
|
|
全自動伺服定位組合,速度快,產能高,最大產速11 sec/cycle
|
|
|
|
全自動張力控制,裁切長度穩定精準,精度為 ± 1 ㎜
|
|
|
|
一、異於低廉作法(結構大量採用鋁擠型,組裝容易,但結構鬆散,易晃動);骨架採型材燒焊、除渣、除銹、物理加工+表面塗裝處理,雖工序繁瑣,但堅固耐用,美觀大方
|
|
|
二、吸吊機為「單側雙立柱」型式,並相互連結結構,吊頭移載時晃動小,壽命佳,對位精度高,可高速移載
|
|
|
|
搭配獨特的快速換模系統,有效降低轉換製程的時程,且降低轉換過程中錯誤發生的機會
|
|
|
|
一、PLC人機介面圖控式操控作業平台,淺顯易懂,方便輸入資料及設定系統,且異常自動偵測及異常自動顯示功能,故障排除輕而易舉
|
|
|
二、設有雷射標線儀於人員疊置台,利於人員對位置放操作
|
|
|
|
移載式交換置物台,大幅縮短換料時間,備料容易且安全
|
|
|
|
立體化設計,有效降低廠房空間需求與建造成本,空餘空間可作其他製程或備料室使用
|
|
|
|
於移動機台上/周邊 設有安全護罩、安全霸、緊急停止按鈕、急停感應桿、安全拉繩、類光幕設計…等,落實妥善的安全防護設計,避免工傷發生
|
|
|
選用系統
一、自動基板裁剪線
二、鋼板刷磨清洗機
三、4軸式銅箔備料發送系統
四、自動PP分離糾邊引取系統
五、快速交換板系統
六、鎢鋼裁切系統
七、鏡板物流系統
八、底板暫存系統
九、自動牛皮紙裝卸系統
規格
迴
回流线流程图
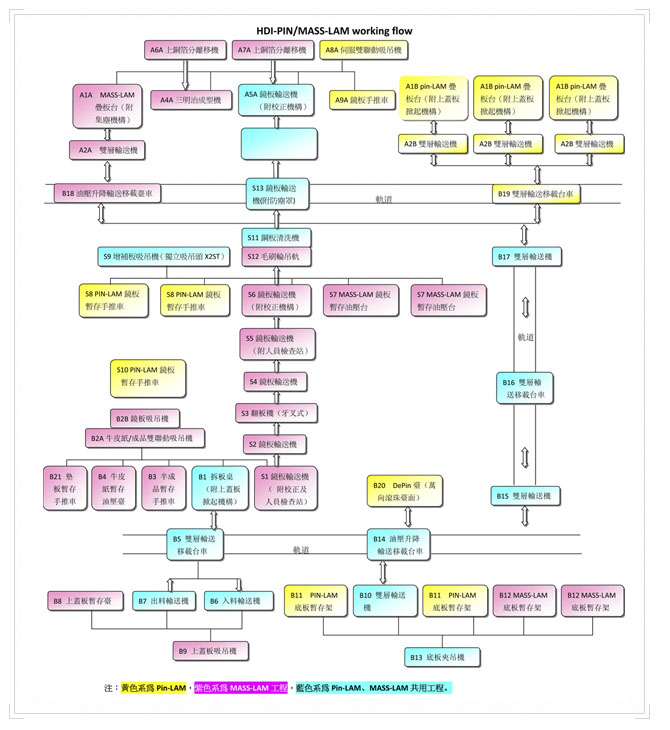
回流线layout
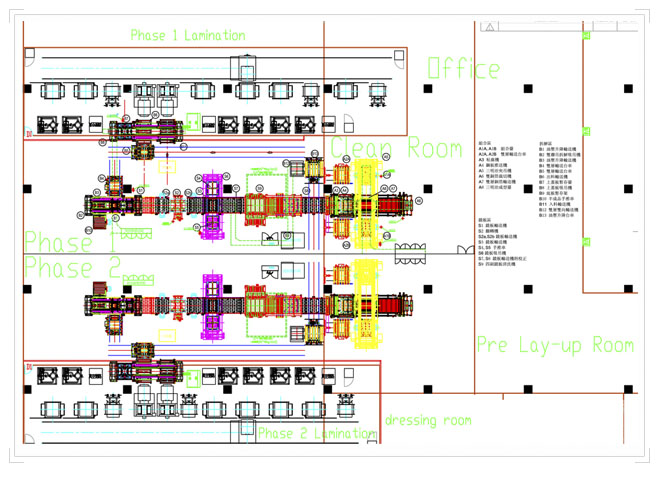
回流线时序图
|